The key is Komatsu Forest’s fleet management system MaxiFleet, which makes it possible to remotely support the customers and thereby reduce the personal meetings, during this period, to prevent the virus from spreading.
“Working from home I can make a quick check how many active machines are out there, if there are any alarms and see if there is anything we need to take care of”, Geddes says.
During the covid-19 pandemic, forestry is, as mentioned, an essential business. During this period the Forest Industry have changed the specification of the wood to adapt for alternative production, and from his home office Geddes can easily help the customers change the bucking instructions for the harvesters.
“During the pandemic the need for pallets has increased so we can have more logistics for medical supply”, Geddes explains. “It is important work and it feels good to know that we can contribute to that.”
MaxiFleet makes it possible to monitor machine’s status, localise machines, optimise the machines as well as support them remotely. MaxiFleet has always been used as a strategical planning tool for Geddes and his team, but the benefits of the system becomes even more apparent now during the crises. “It is the combination of the system, together with the personnel behind it, that makes it possible to give the customer the possibility to keep up optimal performance and back them up in time of need”.
To prevent the virus from spreading, the UK team has installed MaxiFleet in a used machine that is going to be delivered to a customer. By doing so they can set up the machine and complete the operator training remotely – to avoid the time that they usually would spend together in the cab.
“In spite of the lockdown, we can keep our customers happy and perform the same level of support as before - without MaxiFleet it would have been impossible”, Geddes concludes.
MaxiFleet keeping supply lines open during lockdown
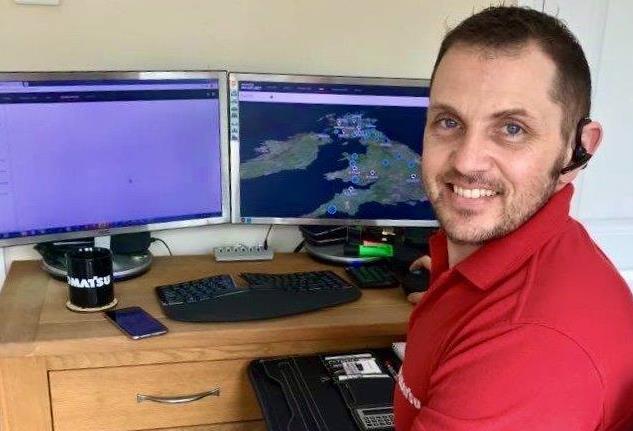
Smart Forestry
April 16, 2020
In UK there is a lockdown during the Covid-19 pandemic and only essential business can be up and running. Forestry is accounted for as an essential business. Still, Komatsu Forest Ltd have taken precautions and let most of the staff in the offices work from home. Talking to Service Technician & IT Training specialist John Geddes, we learn how it is possible for him to help the customers keep optimal performance of their machines, whilst working from home.